Understanding Injection Molded Prototypes: Revolutionizing Metal Fabrication
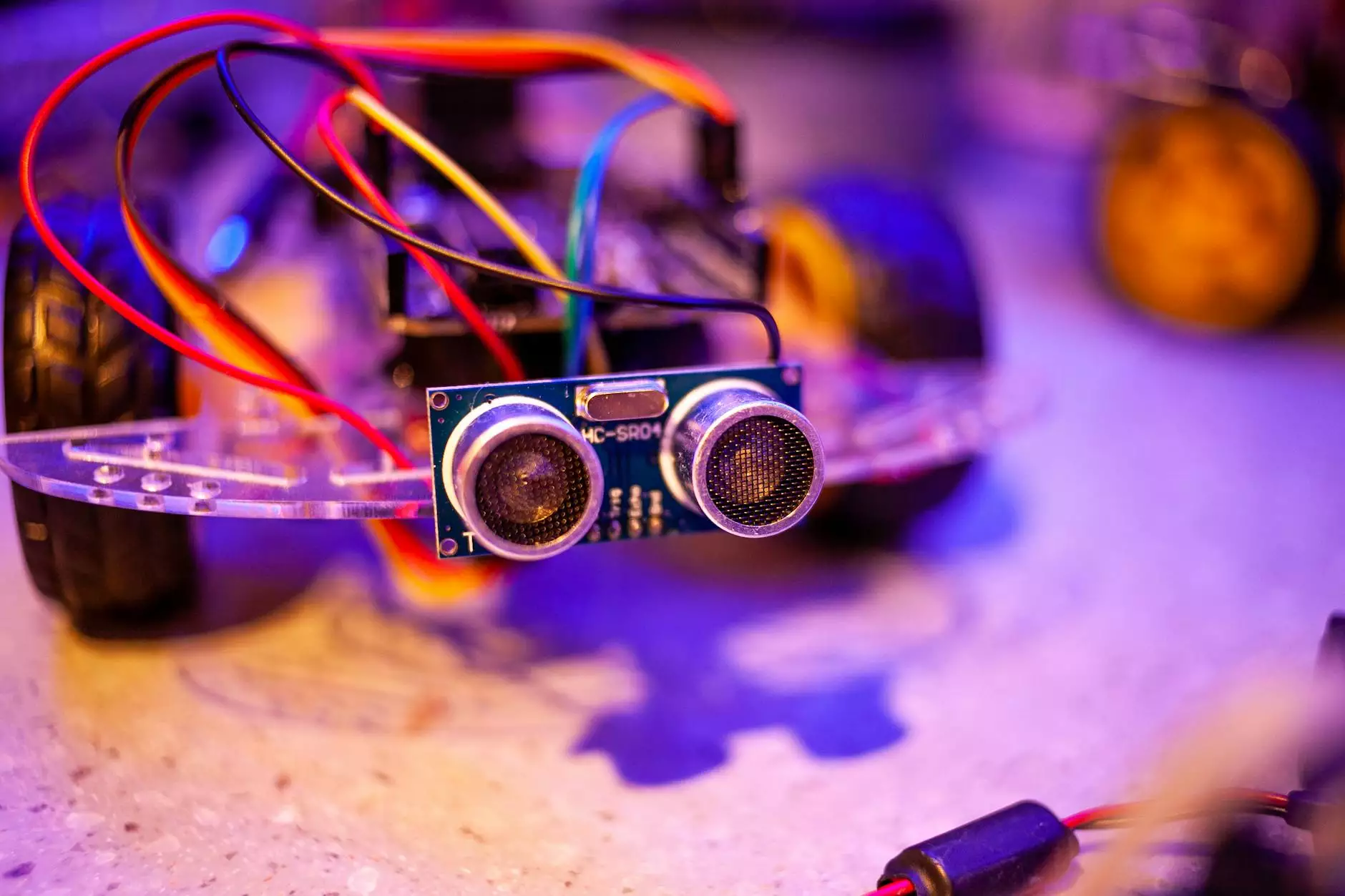
In the world of metal fabrication, precision and efficiency are critical to success. One of the most transformative techniques in this sector is Injection Molded Prototypes. This innovative process not only streamlines production but also enhances design flexibility, allowing businesses to meet ever-evolving consumer demands with ease.
What Are Injection Molded Prototypes?
Injection molded prototypes are preliminary models created through the injection molding process. This method involves injecting molten material into a mold to produce a specific shape, which can then be used for testing and evaluation before mass production. These prototypes serve as a critical step in the product development lifecycle, demonstrating form, fit, and function accurately.
The Injection Molding Process Explained
The injection molding process typically follows these steps:
- Material Selection: The first step involves choosing the right thermoplastic or thermosetting material suitable for the final product's function.
- Mold Design: Designers create precise molds based on CAD designs to ensure exact replication of the intended product.
- Injection: The chosen material is heated until it flows, then injected into the mold under high pressure.
- Cooling: After injection, the material cools and solidifies, taking the shape of the mold.
- Demolding: Once solidified, the prototype is removed from the mold for inspection and testing.
Benefits of Using Injection Molded Prototypes in Metal Fabrication
Utilizing injection molded prototypes in metal fabrication yields numerous benefits:
1. Enhanced Design Verification
Prototyping allows designers to evaluate their concepts physically and identify design flaws early. This iterative process leads to a final product that meets customer specifications and quality standards.
2. Reduced Time-to-Market
By streamlining the prototyping phase, businesses can expedite their overall product development cycle. Injection molded prototypes help in conducting faster iterations, ensuring that the final product is market-ready sooner.
3. Cost-Effectiveness
While the initial investment in mold creation may be significant, the long-term savings through decreased production waste and fewer modification costs make injection molding a cost-effective solution.
4. Material Versatility
Injection molding can accommodate a wide range of materials, from various plastics to metals. This versatility allows manufacturers to select materials that best suit their product requirements.
5. Scalability
Once a prototype is validated, the same mold can be used for mass production. This scalability ensures that production processes remain efficient without compromising quality.
Applications of Injection Molded Prototypes in Various Industries
The flexibility and effectiveness of injection molded prototypes make them applicable across many industries, including:
- Automotive Industry: Used for creating precise components like dashboards, housings, and trims.
- Consumer Electronics: Ideal for prototypes of casings, buttons, and connectors, allowing for fine detail and functionality testing.
- Medical Devices: Ensures that prototypes meet stringent regulatory requirements while also testing ergonomic designs.
- Aerospace: Facilitates the creation of lightweight yet strong components crucial for aircraft performance.
- Toys and Games: Allows for rapid iteration of design, ensuring safety and compliance with regulations.
Challenges in Injection Molding and How to Overcome Them
While injection molded prototypes offer significant benefits, there are challenges that businesses must navigate:
1. High Initial Costs
The cost of creating molds can be substantial, particularly for complex designs. However, utilizing advanced technologies like 3D printing for initial prototypes can lower expenses before committing to traditional molding.
2. Design Limitations
Some complex geometries may be challenging to achieve using injection molding. Collaborating with experienced designers can help optimize designs for manufacturability.
3. Source Material Variability
Variability in raw materials can impact the quality of the prototypes. Working with reputable suppliers and conducting thorough material testing can mitigate this issue.
Choosing the Right Partner for Injection Molded Prototypes
Selecting the right manufacturing partner is crucial. Here are some tips to guide your decision:
- Expertise: Look for a partner with proven experience in injection molding and prototype development.
- Technology: Ensure they use advanced technology to create precise molds and prototypes.
- Communication: A good partner should maintain open lines of communication to keep you informed throughout the process.
- Quality Assurance: Check if they have quality control measures in place to ensure the prototypes meet necessary standards.
Conclusion
In conclusion, injection molded prototypes have become an essential tool for metal fabricators and manufacturers across industries. Their ability to showcase the viability of designs, reduce costs, and shorten time-to-market make them invaluable in a competitive landscape. By overcoming challenges and choosing the right partners, businesses can leverage this technology for unprecedented success.
As you consider integrating injection molded prototypes into your operations, remember that investing in this technology is an investment in the future. With companies like Deep Mould leading the charge, the opportunities available are limitless.