The Essential Role of Label Applicators in Modern Business Operations
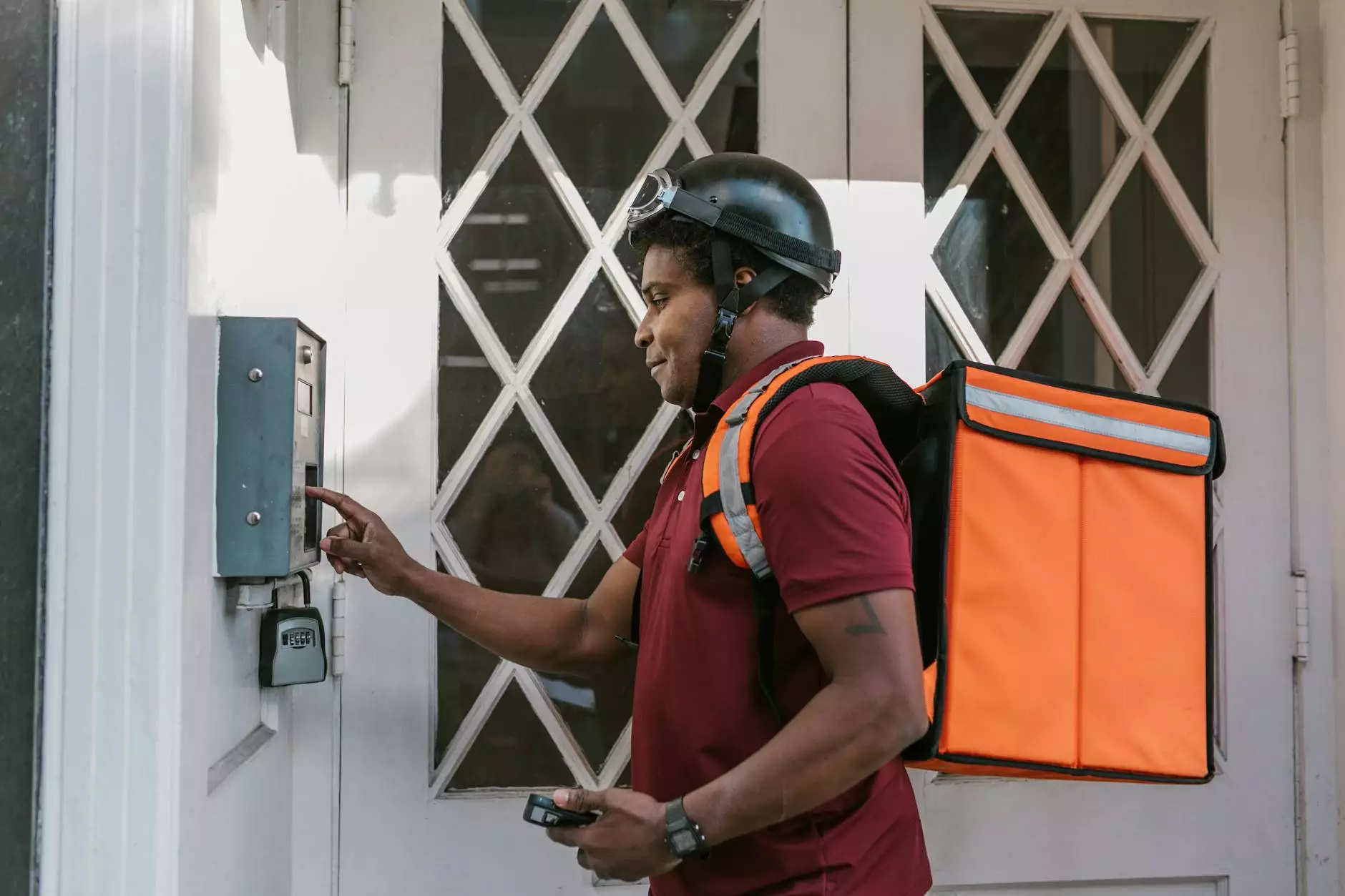
In today’s fast-paced business environment, efficiency and accuracy are paramount. Companies across various industries are constantly on the lookout for innovative tools that can enhance productivity. One such tool that has become indispensable is the label applicator.
Understanding Label Applicators
A label applicator is a machine designed to apply labels to products, packages, or containers quickly and accurately. These devices are increasingly becoming vital in sectors such as manufacturing, logistics, and retail. They help businesses save time, reduce labor costs, and improve the overall quality of their operations.
Benefits of Using Label Applicators
The integration of label applicators into business operations comes with a myriad of benefits:
- Increased Efficiency: Label applicators can operate at high speeds, applying labels much faster than manual labor. This acceleration translates to significantly higher output, especially in high-demand environments.
- Consistency and Quality: Unlike human workers, label applicators deliver consistent results. This uniformity is critical when maintaining quality standards across large batches of products.
- Cost-Effectiveness: By automating the labeling process, companies can reduce labor costs while also minimizing errors that could lead to expensive rework.
- Versatility: Modern label applicators can handle various label types, sizes, and materials, making them suitable for a wide range of products.
- Enhanced Tracking: Many label applicators are compatible with serialization and barcode technologies, aiding in inventory management and tracking efficiency.
Types of Label Applicators
Understanding the different types of label applicators available can help businesses choose the right equipment for their needs:
1. Manual Label Applicators
These are simple, handheld devices that allow operators to apply labels manually. They are ideal for small production runs and are cost-effective solutions for businesses just starting out.
2. Semi-Automatic Label Applicators
Semi-automatic applicators require some manual intervention but can apply labels much faster than a person could alone. They are perfect for mid-sized operations where budget and efficiency are both considerations.
3. Fully Automatic Label Applicators
Fully automatic systems are integrated into production lines, applying labels at high speeds without any manual input. These are ideal for high-volume manufacturing settings where efficiency is crucial.
4. Custom Label Applicators
For unique labeling needs or businesses with specialized products, custom label applicators can be designed. These systems cater to specific requirements that standard machines might not fulfill.
Key Features to Consider When Choosing a Label Applicator
Selecting the right label applicator for your business involves understanding the features that will meet your operational needs best:
- Speed: Assess how fast the applicator can operate compared to your production requirements.
- Label Size Compatibility: Ensure that the applicator can handle the range of label sizes you intend to use.
- Ease of Use: Look for user-friendly controls and easy setup to minimize the learning curve.
- Durability: A machine that can withstand the rigors of your production environment will save money on repairs and replacements.
- Maintenance Requirements: Review the maintenance needed for the applicator to ensure it fits your operational capabilities.
Implementing Label Applicators in Your Business
To make the most of label applicators, businesses should follow these practical steps for implementation:
1. Assess Current Operations
Begin by evaluating your current labeling process. Identify bottlenecks, costs, and time consumed to get a clear picture of how a label applicator could enhance productivity.
2. Determine Requirements
Based on the assessment, outline the specific requirements for the applicator, including speed, size compatibility, and any integration needs with existing systems.
3. Research and Select the Right Model
With requirements defined, research various models. Request demos and seek feedback from other businesses that have made similar investments.
4. Train Your Team
Once the applicator is chosen, train your staff thoroughly to ensure they can operate and maintain the machine effectively. A well-trained team will make the transition smoother and enhance productivity.
5. Monitor and Adjust
Post-implementation, continuously monitor the machine’s performance and make adjustments as necessary. Regular maintenance checks will also keep your systems running smoothly over time.
Innovations in Labeling Technology
The world of labeling technology is evolving rapidly. Here are some recent innovations in the realm of label applicators that could influence your business:
- Smart Labeling: Advanced applicators equipped with AI can learn labeling patterns and optimize for faster output.
- Integration with IoT: Internet of Things technology allows label applicators to connect with other machines and systems for real-time data sharing and improved workflow.
- Sustainability Features: New models are increasingly designed with eco-friendly materials and processes, appealing to environmentally-conscious businesses.
- Enhanced User Interfaces: Modern systems come with touch-screen interfaces and intuitive design, making them easier to operate and manage.
Conclusion
The adoption of label applicators can significantly transform your business operations. By improving speed, quality, and consistency, these devices can help you stay competitive in a demanding market. Furthermore, with ongoing innovations, incorporating a label applicator will only enhance its value proposition. To achieve optimal results, partnerships with trusted suppliers, such as Omega Brand, can provide you with cutting-edge solutions tailored to your needs. Investing in a high-quality label applicator today could lead to the success of your business in the future.